LSU Innovation in Fuel Cell Technology for Electric Cars and Trucks Draws Interest from General Motors, Brings Toyota to Campus
January 20, 2021
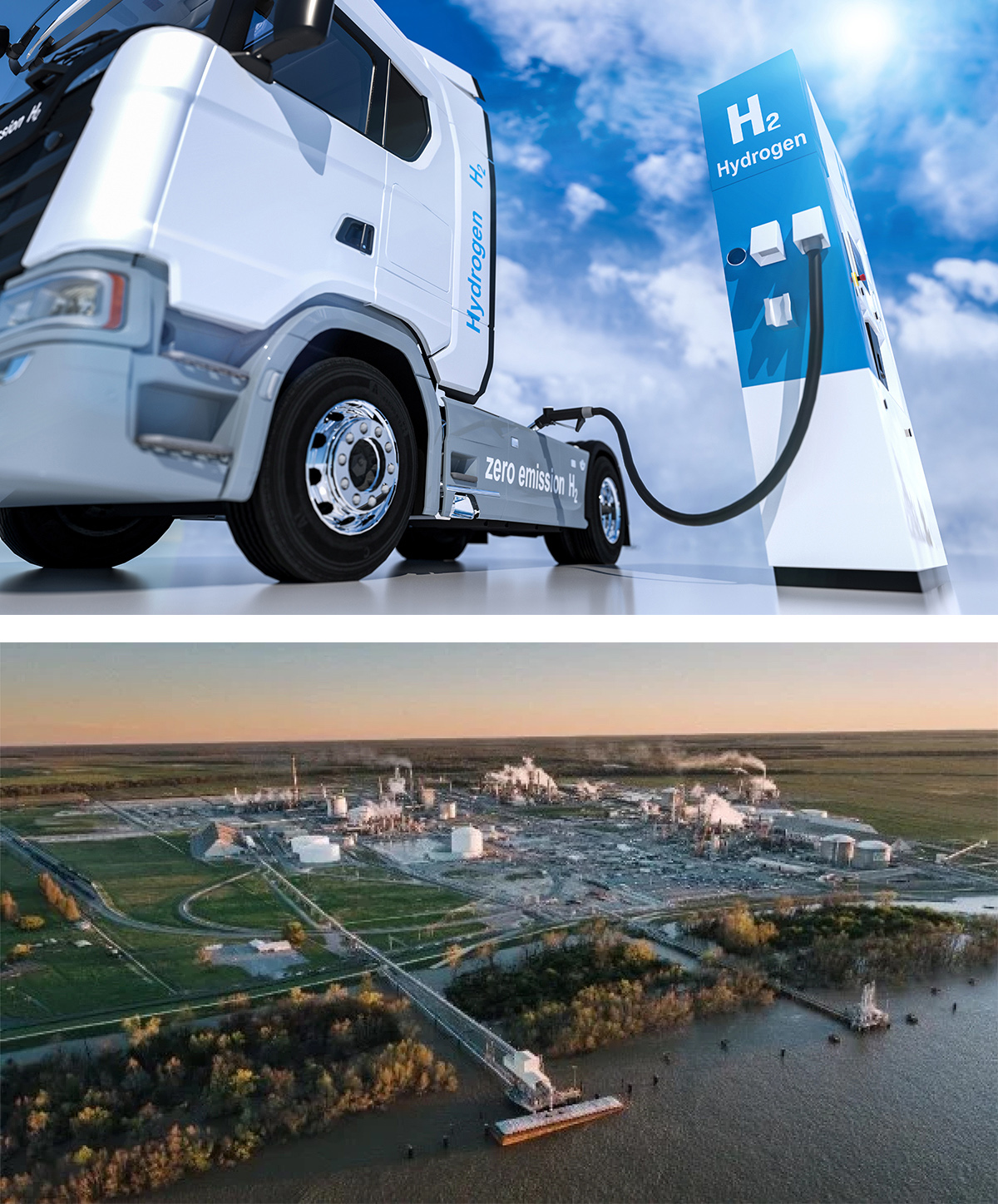
Louisiana is poised as a leader in hydrogen production to drive fuel cells. Both because of high natural gas production (hydrogen can be produced by steam-reforming methane, the primary component of natural gas, which currently dominates production at 85%) but also as a chemical industry hub, with a workforce and knowledge base to match. CF Industries (above) is building an electrolysis-based (zero-carbon) hydrogen plant to make ammonia for fertilizers in Donaldsonville, Louisiana. They could potentially also make hydrogen for fuel cell vehicles.
Higher power densities could transform future, green travel—including by air—and Louisiana is poised to lead in zero-carbon and low-carbon chemical fuel manufacturing.
Fuel cells are maturing as an environmentally friendly technology to power electric cars and trucks. It also holds advantages over battery-driven vehicles. Fuel cells do not have to charge for several hours, and recent research is enabling higher power densities, making the technology lighter, cheaper, and more portable—with more room for people and cargo. Companies, such as Airbus and HyPoint, are even exploring fuel cells for planes, including commercial passenger airliners for up to 200 passengers—a mode of transportation long thought impossible to decarbonize. While taking a single long-haul flight on today’s jet-fueled airplanes generates more carbon emissions than the average person in many countries around the world produces in a whole year (or some do in a lifetime), fuel cell-driven travel emits nothing but water. Since transportation alone represents close to 40% of U.S. energy consumption (25% worldwide), it’s easy to see how fuel cells aren’t “fool cells,” as Tesla CEO Elon Musk has joked, but a valid and complementary alternative to battery-driven electric vehicles—especially when those vehicles are large and have to go far, and the batteries that would be required to do so—based on today’s technology—would get too big, heavy, and expensive to be practical. Just as we have both gas and diesel engines, batteries and fuel cells meet different needs. Together, these green technologies could power almost all transport in the future.
Fuel cell vehicles began hitting the road in recent years. Toyota, Hyundai, and Honda now sell or lease fuel cell vehicles in California, and fuel cell buses are transporting people in several cities around the globe. General Motors has demonstrated the fuel cell truck prototype Chevrolet Colorado ZH2 Concept, which is powered by its Hydrotec fuel cell technology, and recently announced that it also will supply fuel cells for Nikola Motor’s Class 8 trucks.
LSU researcher Christopher Arges, an assistant professor in the Cain Department of Chemical Engineering, is helping to make fuel cell technology even more powerful. Today’s commercially available fuel cell vehicles, such as the Toyota Mirai, use low-temperature polymer electrolyte membranes (PEMs). Assembled into stacks, they need to be cooled with a radiator and sometimes also hydrated by a humidifier to work. To address these limitations, Arges and his team have invented a new type of extreme-temperature PEM that requires neither. This discovery holds great promise in increasing the power density in vehicles where multiple fuel cells could be stacked close together without the heat they produce turning into a performance problem. Arges’s PEMs actually perform better in the kind of heat you’d need to bake a pizza (200-250 C) than near the temperature of boiling water (100 C)—the current limitation of low-temperature PEMs. They also perform at very low temperatures, down to -70 C, about as cold as it ever gets in Siberia.
“Fuel cell technology is well suited to the future of clean, green travel and the impact of Chris’ research is huge.”
Yu Seung Kim, fuel cell research team leader, Los Alamos National Laboratory
“Fuel cell technology is well suited to the future of clean, green travel and the impact of Chris’ research is huge,” said Yu Seung Kim, a team leader of fuel cell research at Los Alamos National Laboratory, which has been working on the technology since the 1970s. “Low-temperature fuel cells still have critical issues and the innovative concept of running fuel cells under hot and dry operating conditions will solve many of them.”
In October 2019, representatives from Toyota came to LSU’s main campus in Baton Rouge, Louisiana to visit Arges’s lab and learn more about his work. Toyota recently announced plans to build heavy-duty fuel cell trucks for the U.S. market and both Toyota and General Motors attended a Department of Energy workshop Arges moderated last September.
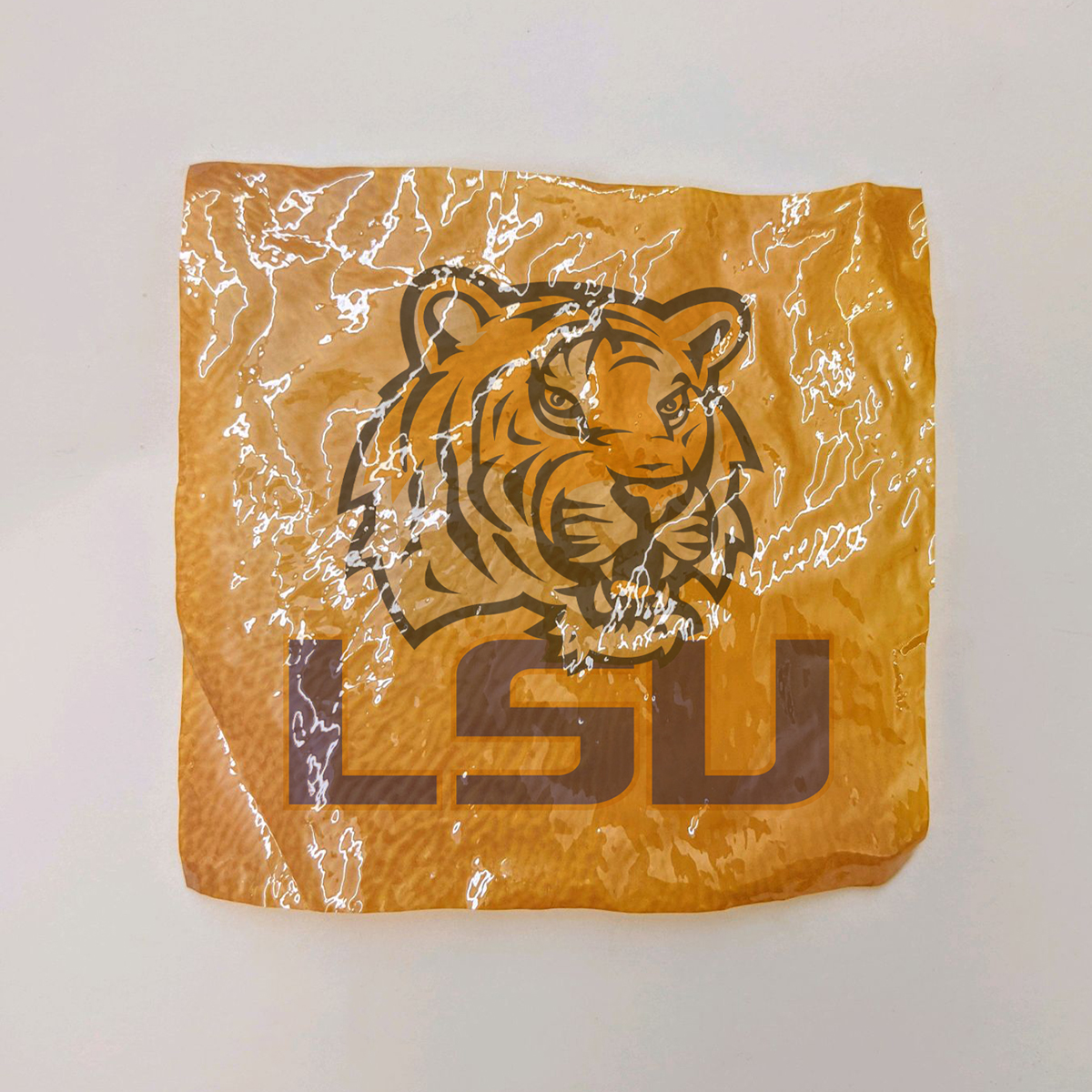
The patent-pending high-temperature polymer electrolyte membrane (PEM) developed by Chris Arges and his team at LSU solves multiple problems that plague the low-temperature PEMs used in fuel cell vehicles today. The PEM is transparent and only 35 micrometers thick (1 micrometer is a millionth of a meter), which is why the LSU logo, printed on a piece of paper underneath, appears through it.
– Photo courtesy of the researchers
“It’s critical for researchers like Chris to be working with someone like us who’s an integrator,” said Craig Gittleman, engineering group manager for fuel cell materials and analysis at General Motors. “You cannot develop new technology in a black box. You have to look at membranes in combination with other things as far as performance, durability, and overall cost.”
Gittleman has been working on fuel cell development at General Motors for 21 years. He sees opportunities for high-temperature PEM fuel cells in large trucks and heavy-duty applications where lots of low-temperature PEM fuel cell stacks would require large and expensive radiators to keep them cool enough to operate. He also sees advantages in using membranes that can perform at below-freezing temperatures, such as Arges’s PEMs, since General Motors is “not interested in developing a product we can only sell in certain parts of the world,” such as in temperate California.
Operating fuel cells at high temperatures comes with challenges of its own, however. Going from cold to very hot and then back to cold again can cause stress for gaskets and seals and other materials in the fuel cell stack that would expand and shrink, changing the amount of compression in the stack and causing the materials to grow weak over time. This could be solved with better and more expensive gaskets and seals, Gittleman noted. Meanwhile, there are also inherent advantages to operating at higher temperatures. The platinum-based catalysts General Motors and other companies use actually degrade less rapidly in dry conditions enabled by high temperatures, and the fuel cells would be less sensitive to contaminants. Finally, the water within the fuel cells, which is generated as part of their normal operation, would remain in a vapor state at high temperatures rather than a liquid that can flood the system and jeopardize fuel cell performance.
“I see several potential benefits in Chris’s work,” Gittleman continued, having recently invited Arges to give a virtual talk to his research group. “I like his approach to performance and appreciate that he’s looking at different materials to meet specific needs.”
“I see several potential benefits in Chris’s work.”
Craig Gittleman, engineering group manager for fuel cell materials and analysis, General Motors
A major challenge for the proliferation of fuel cell cars is the requirement to build a vast new infrastructure. In order to operate, fuel cells need oxygen and hydrogen. Oxygen is in the air, so that supply is free and readily available, while hydrogen (as H2)—although the most abundant molecule in the universe—must be made here on Earth by pulling H atoms from water or fossil fuels. This can happen with a zero-carbon footprint through water electrolysis driven by wind or solar power, or by steam-reforming methane, the primary component of natural gas. In the latter process, methane (CH4) reacts with steam (H2O) to produce hydrogen (H2) as well as carbon monoxide (CO) and small amounts of carbon dioxide (CO2). Steam-reformed methane generates over 80% of the hydrogen used today, and although this process produces carbon emissions, it’s much less than from gasoline production and combustion (and the carbon dioxide could be prevented from going into the atmosphere).
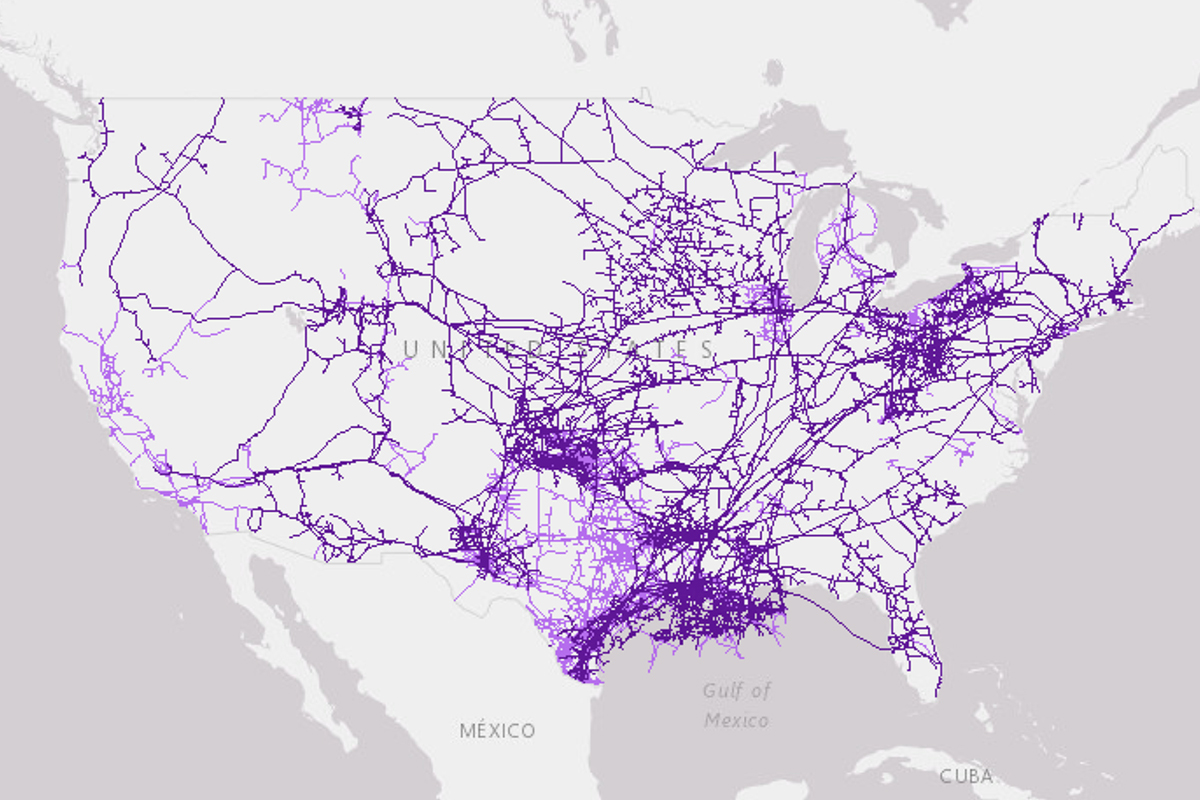
Map of interstate (dark purple) and intrastate (light purple) natural gas pipelines in the U.S. You can barely see Louisiana, which is the third-largest natural gas producer in the nation, covered in purple lines. Since methane, the primary component of natural gas, can be used to make hydrogen for fuel cells, Louisiana might offer a pragmatic and near-term bridge to net-zero carbon emission technologies through its large natural gas extraction, processing, and distribution industries.
As the third-largest U.S. producer of natural gas, after Texas and Pennsylvania, Louisiana
is a leader in hydrogen production and use in chemical manufacturing. Every seventh
job in Louisiana is in the chemical industry and having that workforce, knowledge,
and experience in the state matters to large companies such as CF industries, the
world’s largest ammonia producer, which is building a new electrolysis-based green
ammonia plant in Donaldsonville, Louisiana.
Ammonia, the third-largest chemical manufactured globally and used in fertilizers,
requires hydrogen as a feed stock, or raw material. Water electrolysis plants, like
the one CF Industries is building, can generate the hydrogen fuel needed for fuel
cell vehicles in addition to meeting demand for ammonia production.
“Louisiana is very well positioned to ‘jump start’ a broader, more integrated hydrogen economy," said David Dismukes, executive director of the LSU Center for Energy Studies. “There is role for Louisiana to play since we have considerable natural gas reserves that are still very economic.”
Not only are fuel cells poised to transform the transportation sector, they can also be used to generate power for buildings, homes, and manufacturing facilities. They can power forklifts in large distribution centers, such as Walmart and Amazon, that don’t have time or patience for battery recharging but also cannot tolerate emissions from combusting fossil fuels. CF Industries expects hydrogen to provide 20% of the world’s energy by 2050, compared to less than 1% today.
“ As the third-largest U.S. producer of natural gas, after Texas and Pennsylvania, Louisiana is a leader in hydrogen production and use in chemical manufacturing. ”
While some companies, such as CF industries, GM, Toyota, and the aircraft company ZeroAvia are eager to reduce their carbon footprint as much as possible and are looking to hydrogen derived from water-electrolysis, Arges believes hydrogen from steam-reformed methane will be an important and practical bridge to wider adoption of fuel cell technology.
“If we were to move to all hydrogen-based vehicles, it would cost something like 15 trillion dollars to build the necessary infrastructure from scratch,” Arges said. “While California has been a leader in terms of refueling stations, we have a clear chicken-and-egg problem. What came first, the vehicle or the refueling station? In Japan, the government is actually building hydrogen refueling stations. And Tesla understands this problem—they’re building charging stations for their own vehicles. This infrastructure challenge isn’t unique to fuel cells, but we need solutions that are pragmatic and near-term to make it possible for a lot more people to buy and drive fuel cell vehicles. And running fuel cells on hydrogen from natural gas seems to fit the bill.”
Another possible bridge technology would be to put onboard reformers on trucks that could “gas up” on methanol and make hydrogen en route—this would also take up less room on the truck than a pure hydrogen system.
“We make methanol in Louisiana and you could take a gasoline station and retrofit it to pump methanol whereas you can’t really modify a gasoline station to pump hydrogen gas,” Arges argued. “Methanol is cheap, and you’d still be reducing carbon emissions, so this could be another bridge to fuel cell proliferation and reduction in greenhouse gas emissions.”
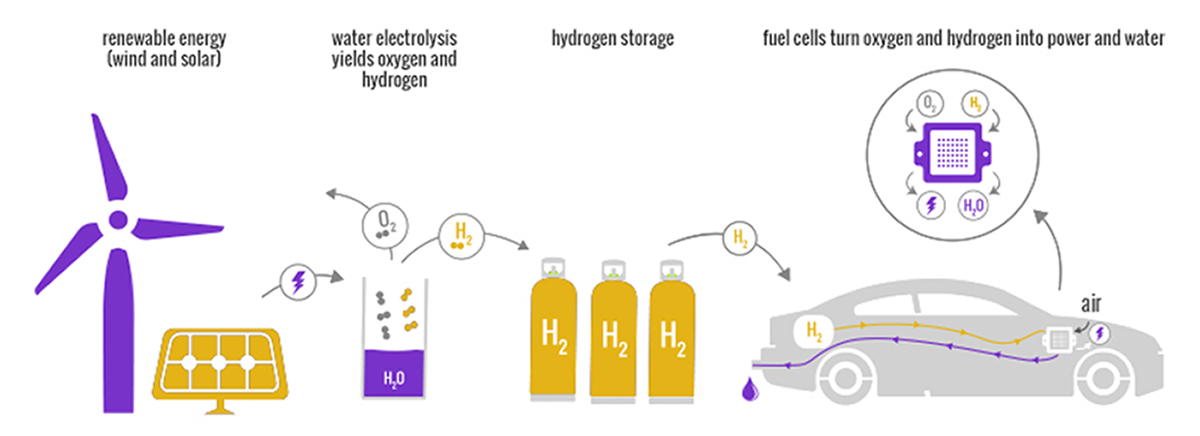
Fuel cells, an alternative to batteries and internal combustion engines, can enable clean, green travel as they only require oxygen and hydrogen to produce electricity, and only emit water. While Toyota already sells a fuel cell passenger vehicle in the U.S., the Mirai, the company is also looking to produce heavy-duty fuel cell trucks for the American market. Besides long-haul trucks and passenger vehicles, fuel cells are ideal to power forklifts in enclosed warehouses (think Amazon and Walmart) where carbon monoxide or carbon dioxide emissions from regular combustion engines would be dangerous, and batteries that take hours to charge might not be practical as part of a continuous 24/7 operation.
– Graphic elements courtesy of Toyota
Currently, hydrogen made from water electrolysis is equivalent to paying $7 at the pump, while hydrogen from methane (natural gas) is about $2. Through further research and development, the price of the former is likely to come down, but in the meantime, hydrogen from methane and methanol would actually work better in Arges’s high-temperature PEMs than the low-temperature PEMs currently on the market, which cannot tolerate residual amounts of carbon monoxide.
“No one wants to pay $7 here in the U.S.,” Arges argued. “But if you talk to Toyota and Nikola Motor, they want to use renewable hydrogen from water electrolysis because it jives with their corporate plan to reduce carbon emissions. Meanwhile, companies like Advent and Ser Energy advocate for hydrogen from methanol for the time being—and for flexible fuel cell systems, meaning they can run on hydrogen from water or from fossil fuels.”
“Louisiana will have an important role in the hydrogen economy and in U.S. Department of Energy initiatives such as Hydrogen at Scale.”
Chris Arges, assistant professor in the LSU Cain Department of Chemical Engineering
The U.S. Department of Energy is currently looking at distributing hydrogen from both sources through the existing natural gas pipeline infrastructure, which in large part is located in Louisiana, which has the highest concentration of natural gas pipelines in the country.
“We’re the epicenter, and Lake Charles sets the price of natural gas for the nation,” Arges said. “So, Louisiana will have an important role in the hydrogen economy and in U.S. Department of Energy initiatives such as Hydrogen at Scale.”
One part of the Hydrogen at Scale (H2@Scale) program explores hydrogen as a way to store energy from renewable sources. If the sun is shining and the wind is blowing, solar panels and wind turbines might produce more energy than is needed in the grid. The excess electricity could be used to electrolyze water to produce hydrogen, which then could be stored and used later—on demand—using a fuel cell, like at nighttime or when the wind dies down, or in winter when the days are shorter and there is less sun. Lengthy energy storage in the form of hydrogen also beats storage in batteries, which discharge over time. This past fall, the U.S. Department of Energy announced two new consortiums to support H2@Scale: H2New, focused on improving water electrolysis for hydrogen generation, and the Million Mile Fuel Cell Truck. Both were described in detail at the workshop Arges helped moderate.
But really, a million miles?
“Needless to say, we’re not there yet,” Arges said. “But high-temperature PEMs can last 15,000 hours, while low-temperature PEMs are more in the vicinity of 6,000 to 9,000 hours—probably due to adverse effects of liquid water. You’d need at least 40,000 hours to go a million miles, so improving our high-temperature PEM technology seems like the fastest way to get there.”
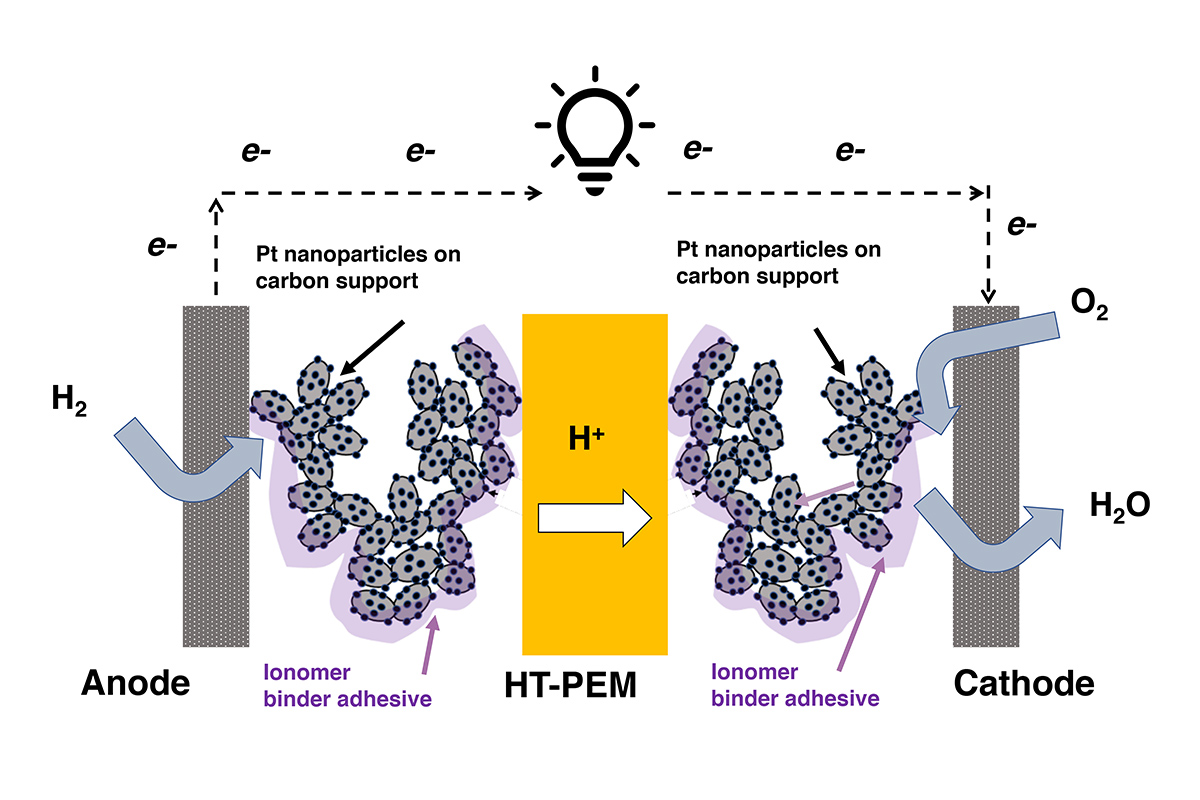
Fuel cells are similar to batteries—they’re configured like “sandwiches,” but with a solid membrane electrolyte instead of a liquid electrolyte as the “cheese” in the middle (the electrodes are the “bread”). The membrane only allows protons to move between the electrodes. Since electrons aren’t allowed through, they’re forced to take another route—around the cell in a circuit, which leads to electricity generation. Arges does not only work on better membranes but also binders.
– Photo courtesy of Chris Arges
Arges and his LSU team hold a $500K award from the Department of Energy’s Advanced Manufacturing Office to figure out how to make more efficient and durable fuel cells in a shorter period of time using machine learning, or artificial intelligence. The researchers have already proven that it’s not just possible; their system is already working and suggesting reasonable solutions—in theory—that Arges and his team can aim for and test in their lab. What makes their project unique is that they’re not only developing new materials for fuel cells (membranes and electrode binders), they’re also validating them in actual fuel cell devices. The machine learning is helping on every level—molecular, material, and in terms of device performance. It’s basic and applied research at the same time.
“This is important because a device has many different materials and components in it,” Arges explained. “It’s got a membrane, two electrodes, two bipolar plates, and lots of different operating parameters and variables that all depend on each other. Machine learning tools can help streamline and accelerate development in this large design space—new materials to formulate that would turn out to be better for an actual fuel cell device.”
Fuel cells are a bit like batteries in that they contain two electrodes (an anode and a cathode). While the electrodes in batteries are separated by a porous separator with liquid electrolyte, in fuel cells, the “meat” in the electrode sandwich is the non-porous membrane, or PEM. Part of the reason fuel cells are expensive is that the electrodes are “dusted” with platinum, which acts as a catalyst and drives the reactions that create the electrical current. The platinum particles require a binder to hold them in place. The binder acts like a glue and also moves ions—atoms or molecules with an electrical charge—between the electrodes and the PEM.
“ By using artificial intelligence, Arges expects to cut a total development time of 15-20 years down to 1-5 years. ”
Arges is quick to point out that promising materials don’t always yield better device performance, depending on how they’re manufactured, combined, and integrated. By using artificial intelligence, Arges expects to cut a total development time of 15-20 years down to 1-5 years.
“Often, new good materials discovered in the lab completely flop once we put them into fuel cell devices,” Arges said. “What really excites me about the machine learning aspects of this project is that these tools can do things that aren’t so intuitive from the human experience and identify relationships that are often hidden and difficult to find. They can suggest solutions and tell us which experiments to prioritize. ‘If you want to get to this point in performance, you need a material with this property and you need to integrate it this way—now, go do it.’ That’s what we’re working on right now.”
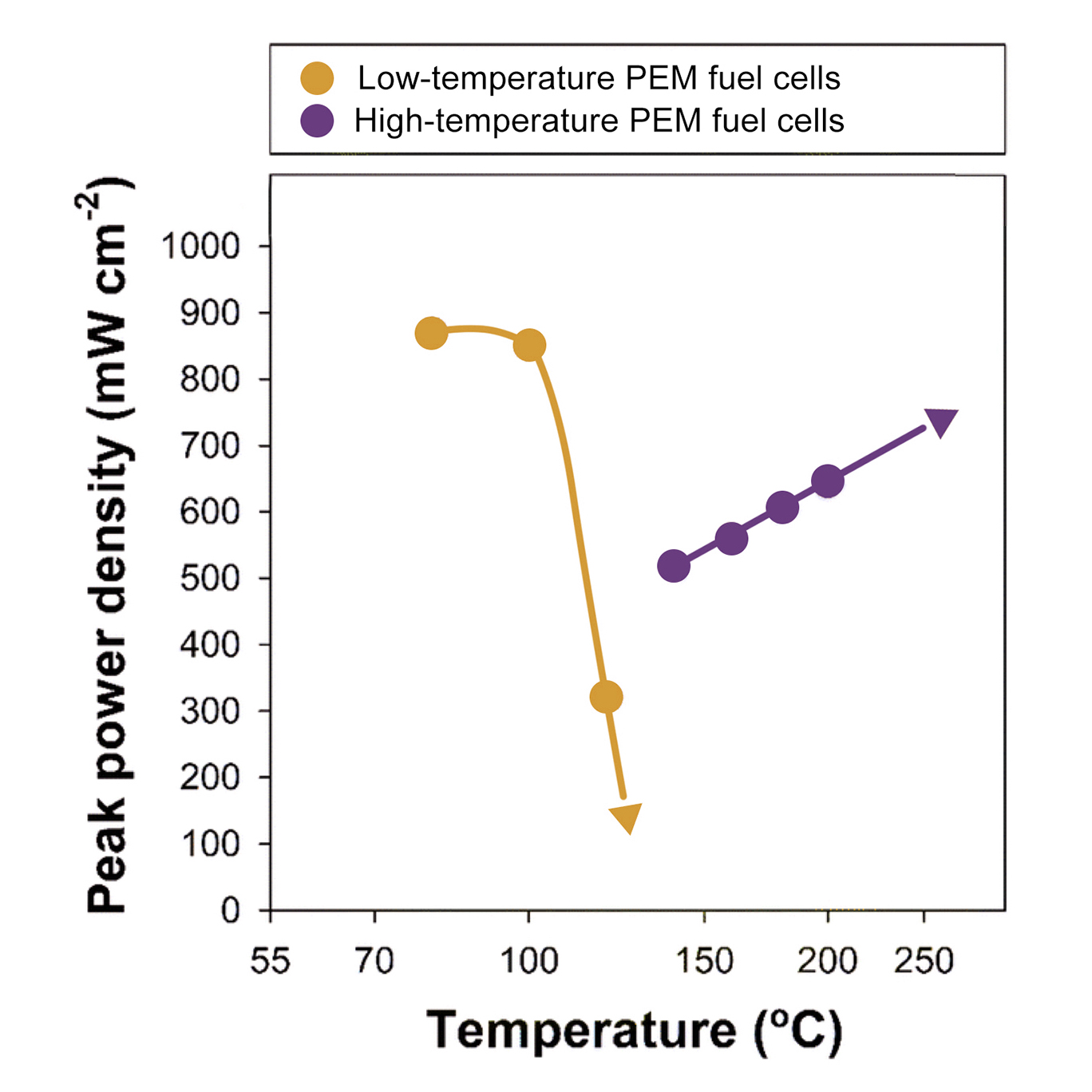
Low-temperature fuel cells can fail somewhat spectacularly at high temperatures, which is why radiators are required to keep them cool in vehicles. In small cars, this isn't a big problem. But in trucks and other large vehicles, the radiators have to be quite big and heavy (meaning they’d be expensive to manufacture, take up a lot of room where passengers or cargo otherwise could go, and the added weight would consume more fuel). Arges’s high-temperature fuel cells perform better than the fuel cells on the market today at extreme temperatures (freezing, boiling) and have been steadily improving. His lab expects to double fuel cell power density within a year.
After recently filing a patent on a high-temperature PEM, Arges’s team has made great strides in developing new electrode binders also. They’ve managed to increase the power density in a fuel cell by a factor of 10 by switching to a new binder. They also anticipate 50% in additional improvement.
“The new binder is working brilliantly, just awesome,” said Arges.
In the low-temperature PEM fuel cells used today, the membrane chemistry and the binder chemistry are the same even though they have different requirements—the membrane has to be mechanically robust, so as not to rip under gas pressure, and only conduct protons (positively charged ions)—not electrons—or the fuel cell shorts out, which could be dangerous—even catastrophic. Also, while the membrane shouldn’t let gas through, which Arges describes as “don’t-cross-the-streams Ghostbusters bad,” the binder needs to be permeable and let gases through quickly. A better binder leads to more efficient use of the platinum catalyst and more functional electrodes, and thus lower fuel cell costs.
By making membranes and binders that can operate efficiently and remain intact at extreme temperatures, Arges is excited about LSU’s current foothold on the frontier of fuel cell technology.
“I’m happy to have Toyota’s support,” Arges said. “When they flew into Baton Rouge and shared their vision for high-temperature systems, it not only validated some of our working hypotheses, but it motivated us further and honed our focus. The high-temperature direction is now garnering more and more interest in the fuel cell community.”
Arges predicts his lab will double fuel cell power density within a year. This would be important for vehicle manufacturers such as Toyota, which hopes to improve their Mirai from 3 kW to 9 kW per liter. A three-fold increase in power density would be transformative and allow fuel cells to go up to 700 miles before filling up on hydrogen again. This would alleviate the burden of building numerous hydrogen gas refueling stations and also lower the manufacturing cost of fuel cell vehicles.
“ By making membranes and binders that can operate efficiently and remain intact at extreme temperatures, Arges is excited about LSU’s current foothold on the frontier of fuel cell technology. ”
The LSU researchers have partnered with Xergy, a membrane manufacturer in Delaware, to scale up their extreme-temperature PEMs. Those membranes will be evaluated independently by Los Alamos National Laboratory and Toyota, which will be testing both performance and durability under relevant automobile conditions.
Arges’s work has so far clinched research grants from the U.S. Department of Energy (both the Basic Energy Sciences and the Advanced Manufacturing Office), the LSU Board of Supervisors LIFT2 program, the Louisiana Board of Regents, the National Science Foundation, and others.
Read More
New paper by Arges’s team in Patterns: “Machine learning for guiding high-temperature PEM fuel cells with greater power density”
LSU ChE Professors Arges, Romagnoli Use AI to Study Fuel Cells
Breaking the Bond: LSU ChE Professor Creates Reactor-Separator to Upgrade Methane
LSU ChE, Chemistry Professors Arges and Kumar Secure $500,000 Grant